Development of an on-line monitoring system for a high power industrial cutting laser
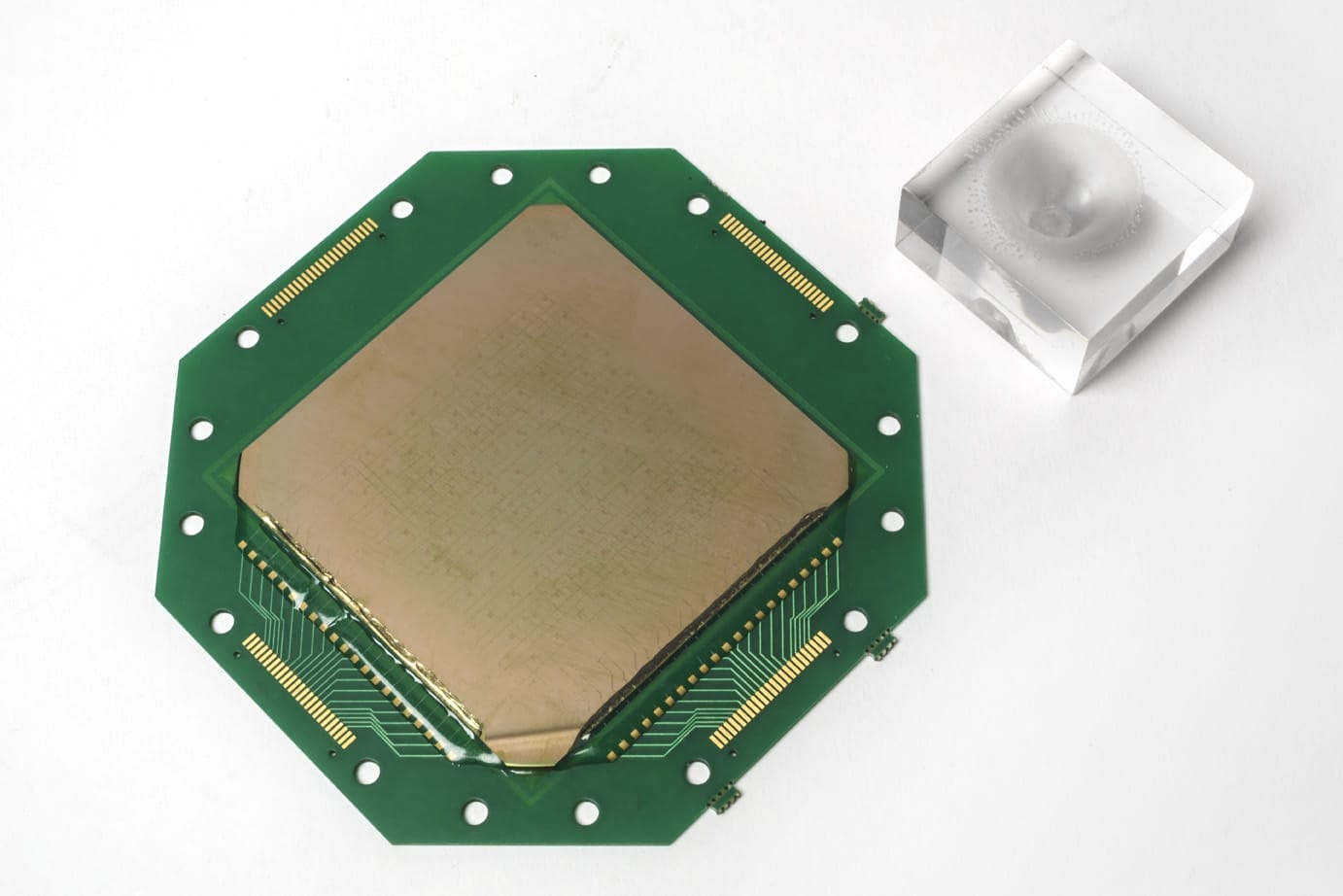
Our client asked:
TRUMPF provides manufacturing solutions in the fields of machine tools, laser technology, electronics and Industry 4.0. It was looking for an on-line monitoring system for a high power (10kW) industrial cutting laser.
The project story:
The challenge that was presented to us was that the lasers need regular trimming in order to maintain their cutting efficiency, but any sensor placed in the beam is instantly destroyed. By monitoring the temperature on the rear of a silicon mirror, we could infer the optical beam profile of the laser. We created a sensor array as an array of diodes that could be integrated into the fabric of the silicon mirror using standard lithographic techniques. Algorithms converted the temperature array data into an accurate representation of the laser beam’s optical profile. Utilising a 2500 pixel MEMS optical beam sensor array, allowed rapid set-up and continuous monitoring of the laser beam’s profile in order to ensure consistent operation of that laser.
Results: deliverables and outcomes
TRMPF still uses this system to continually monitor and auto-trim their cutting lasers.
Industrial markets
Discover the expertise we offer across the industrial market and how we collaborate to solve challenges through R&D.
Innovation services
Find out about Sagentia Innovation’s comprehensive suite of advisory and product development services, tailored to support consumer and industrial sectors.
Contact us
We’d be delighted to discuss your challenges and explore how innovative thinking could help solve them. If you’d like us to get in touch, please complete the contact us form.